SHOP BY
PRODUCT
(Alpha Order)
ABRASIVES
ZEK DISCS
WIRE WHEELS
METAL POLISHING
SEALANT CUT-OUT
AIR
SCRUBBERS
VENTILATORS
ANCHORS,
EPOXY
MASONRY
MADE TO PRINT
STRUT, FITTINGS
CARBIDE,
CHISELS
DUST CONTROL
CUSTOM LENGTHS
DIAMONDS
GRINDER
PACKAGES
DESIGN
& BUILD
METAL FABRICATION
DUST
EXTRACTORS
ACCESSORIES
HEPA VACUUMS
DUST
FANS
VENTILATION
CONTAINMENT
ENCLOSURES
RAM BOARD, TAPE
PLASTIC SHEETING
FLOOR
GRINDERS
GRIND / POLISH
COATING REMOVAL
GANG
BOXES
GENERATORS
INVERTERS
LADDERS
PRESSURE
WASHERS
RECOVERY
SLURRY
VACUUMS
PRESS MACHINES
SURFACE
PREP
FLOOR GRINDERS
DIAMOND TOOLING
| |
Additional
Information
Benefits
|
|
ELIMINATE
REGULATORY CONCERNS
With
increased EPA enforcement of industrial suspended solids many
contractors have been hit recently with large fines. Most
contractors are unwilling to carry the huge financial risk and
liability associated with not cleaning their water. Some
contractors have left the efficiency of wet grinding and face
new operational difficulties with dry grinding.
The
MudHen eliminates your financial liability over regulatory
concerns potentially saving you thousands of dollars, allowing
for water reuse and recycling on site.
|
Applications
|
MudHens
can solve a variety of slurry water issues for different
applications. They are commonly used on stone, ceramic
and glass slurry as well as other slurries that have a high
quantity of suspended solids.
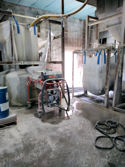 |
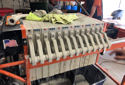 |
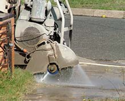 |
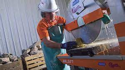 |
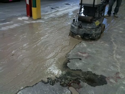 |
Fabrication
Plants |
Walk-Behind
Saws |
Masonry
Saws |
Concrete
Slurry |
Slurry
waters can be effectively treated to be EPA (Environmental
Protection Agency) compliant. Pump trucks, stone and
tile saws, cement and mortar mixers along with industrial
slurries can be treated to remove the vast majority of
suspended solids. The pH can easily be treated to meet
EPA requirements.
The
recycled water can be reused on site to reduce water
consumption. The sludge is collected and compacted for
easy disposal.
For
years concrete wash out slurry has been a challenge.
With a MudHen concrete washout system compliance has never
been easier. All MudHen products are made in the USA.
Application:
Concrete Washout ---
Concrete, Terrazzo, Paint, Stucco, Mortars, Grout, Stone,
Tile, Glass, etc.
SLURRY
SOLUTIONS - INDUSTRIES
WE SERVE |
MINING
& FRACKING |
CONSTRUCTION
& INDUSTRIAL |
METAL
& METAL FINISHING |
READY
MIX WASHOUT |
CONCRETE
POLISHING |
GRANITE
&
STONE FABRICATION |
FOOD
& BEVERAGE |
MASONRY
&
CONCRETE SAWING |
WATER
JET BLASTING |
PRE-CAST |
PETROLEUM |
CHEMICAL |
MUNICIPAL |
GLASS |
CEMENT |
|
|
Sizing - What size
press do I need?
|
If
you’re working in an industry where wastewater is a
byproduct, you’ll need an effective method to treat the
slurry water. A filter press is the perfect solution,
but it isn’t just one size fits all.
It’s
important to consider size before investing in a filter
press. It’s easy to simply choose the biggest option
and assume the filtration process will go smoothly as long as
it isn’t overloaded. But bigger is not always better so
you should choose a filter press after carefully considering
your needs and the application you are using it for.
In
certain applications, cake and water quality can drop if the
press is oversized. Additionally, a filter press than is
too large can make your costs rise, not only with the initial
purchase but when running the machine. Thoughtful design
and pairing with other technologies can reduce the size and
overall cost of your purchase.
BUYING
DECISION - Which Mudhen to Purchase?
Factors
to Consider:
-
How
many gallons of slurry do you need to process per day?
The quantity of solids
that are in the slurry? --- Slurry with less solids
require less filter chambers.
-
PATIENCE
or SPEED? For
slurry with more solids, although all the Mudhens will
do the job, the more collection chambers there are the less time
you'll spend separating and emptying them. For
example, to process 500 gallons
of concrete slurry per hour you'll want to go with a larger
filter press (MH1 or MH2), otherwise you'll be spending
too much time manning the machine (i.e. emptying
plates).
-
Mudhen
Size & Weight - although all 4-Mudhen models are
portable, the Mini and MH1 are smaller and weigh less so
they may be better suited for maneuvering within job
constraints.
COMPRESSOR
SIZE - Air Requirements
-
Dry
filtered air is required to minimize the maintenance on
the system
-
MudHens
can be adjusted to effectively operate in a wide range
of locations and conditions. Minimum CFM is 5,
ideally: 10 CFM.
-
MudHens
are equipped with an air operated diaphragm pump - this
pump requires a minimum of 5 cfm of air to operate with
a tank size between 15 and 30 gallons (an air compressor
with a 15-gallon tank is the
smallest size tank that can operate a MudHen)
-
RECOMMENDED
COMPRESSOR - Mudhens run best using a 15 / 30-gallon air
compressor set between 50 and 80 PSI - see Dewalt
D55168 Compressor (right.) Once properly
adjusted to your filtration requirements and processing
times, the Mudhen may be left to operate
unattended. For crystal clear water output,
efficiency of operation and fast processing times set
the compressor at 50 PSI and adjust it upwards to a
maximum of 80 PSI.
If
you have any questions and are pondering what size or
additional components you may need, please call us - we'll be happy to assist
you: 412
- 605 - 2992.
|
|
|
Operation
|
-
Connect
air compressor hose to Mudhen air fitting
-
Place
slurry line and screener (included) into the container of
slurry
-
Attach
output hose and secure the hose into the container that the
clarified water will flow in
-
Adjust
regulator on Mudhen control panel to 30 PSI
-
Turn
operation controller "on" – the Mudhen will
begin to pump slurry through the unit
-
As
back pressure builds in the Mudhen and the pump slows,
adjust PSI regulator upwards in 20 pound increments.
This is done up to 80 psi, do not and never exceed 80 PSI.
-
Eventually
the Mudhen's pump will stall or you'll hear it trying to
gulp for slurry, this is the indication that the collection
chambers are full of solids or the slurry container is empty
(the pump will not be harmed as it gulps for more slurry to
process.)
|
Leaking
Plates
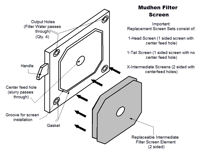
|
Pre-Coating
the Filter Cloths. If
the plates leak while pressure builds, apply more pressure via
the hand jack. Each filter plate or chamber includes (20
filter media cloths with a filter efficiency rating of 5
microns.
The
filter cloths require solids in your slurry to ensure the
efficient operation of a Mudhen (i.e. the chambers will leak if
drinking water is pumped through them.)
Pre-coating
the filter cloths increases their efficiency rating to 1 to .6
microns
Pre-coating
the filter cloths should be your 1st step to ensure the purity
of the liquid being discharged.
|
PRE-COAT
STEP
"GO
SLOW & LONG ENOUGH"
This
step is only for the first filling of the plates. After
the initial release of your first cakes you'll still start the
Mudhen slowly (10 PSI), but only for a few minutes as the filter
cloths are already coated.
As
you observe the clarity of the water being discharged, the PSI
may be gradually increased to the optimal operating setting
between 50 and 80 PSI.
|
Two
(2) Pre-Coat
Methods:
-
Loading
Method - Using your own sediment. Start the Mudhen at
the slowest speed possible (1 - 10 PSI). Depending on
the particle size and volume of sediment in your slurry,
pre-coating times will vary (2 to 40 minutes).
-
Mix
Method - Mix 20 lbs. of diatomaceous earth (or perlite or dicalite)
with 10 gallons of water. Pump this milkshake mixture
through the filter chambers to instantly pre-coat the filter
cloths. You may immediately being normal operation of
the Mudhen using its optimal operating speed of 80 PSI.
Once
the filter cloths are properly coating (as determined by the
purity of the water being discharged), you can increase the PSI
into the press.
If
the water being discharged ever begins to look cloudy simply
reduce the PSI to the pump. This will slow down the intake
of slurry going into the filter chambers while it continues to
pre-coat the filter cloths. Additionally, if speed isn't
too important you can leave the machine operating slowly (i.e.
50 PSI).
|
Caked Solids
Emptying
the filter chambers and dropping the caked plates.
The
powerful 3/4" diaphragm pump (completely adjustable, 0 - 30
GPM or 0 - 100 psi of air) will push and compact the solids in
the filter chambers.
The
filter chambers, held in place within the heavy framework of the
Mudhen, are pressed together with 5000 lbs. of force from the
hydraulic hand pump.
As
the filter chambers fill, pressure gradually increases and the
purity of the liquid being discharged also improves as the
solids fill within the filter chambers.
Once
full (the liquid being discharged will cease to flow), operator
intervention is required to release the dry the caked plates and
empty the chambers.
As
each filter chamber is separated, the caked plates are released
and dropped into the collection tray or a wheel barrel.
|
Drying / Cleaning
Procedure:
- Remove
slurry line from sludge and allow pump to pump air for a
minimum of 5 minutes (the longer it operates the drier the
cake)
- Turn
operation controller to off, adjust air to 30 psi
- Turn
operation controller to dry
- Turn
isolation valve “A” located right below controls to its
off position (ref Operation drawing, above)
- This
will allow more air to travel through the plates
- Water
will sputter out of the output hose
- After 2
minutes open the isolation valve “A”
- Turn
the operation controller to off
- Loosen
the hydraulic jack pressure relief valve
- Separate
the chambers and clean the screens with the enclosed scraper
- After
every 1 to 4 weeks depending on the nature of the slurry –
pressure wash the plates & cloths to ensure open and
clean pores for proper filtering
- DO NOT
LEAVE SOLIDS IN THE MUDHEN FOR MORE THAN 1 TO 2 DAYS –
DOING SO CAN RUIN THE SCREEN CLOTHS INSIDE THE SYSTEM.
END of DAY
CLEANING
At the end of each day
of use it is important to flush out any slurry from the
system. This includes flushing the air pump and the
filtration plates as well as any hoses. This can be done
by directing the clean water discharge hose from the system and
running its clean water right through the Mudhen.
|
|
|
|
|